-
Press release
Cement-free concrete “Tiny House” sets ecological standards
The first “Tiny House“ made of cement-free prefabricated 3d-printed concrete elements was built on a biker track in Beckum, Westphalia, and saved around 70% of CO₂ emissions compared to (cementitious) concrete. Read more!
First cement-free concrete “Tiny House” of 3D-printed parts
Sep 12, 2023
The first 3D-printed modular building made of cement-free concrete has been built in Beckum, Westphalia (Germany), marking the culmination of an innovative project that underlines the potential of a promising new approach to (pre)fabrication.
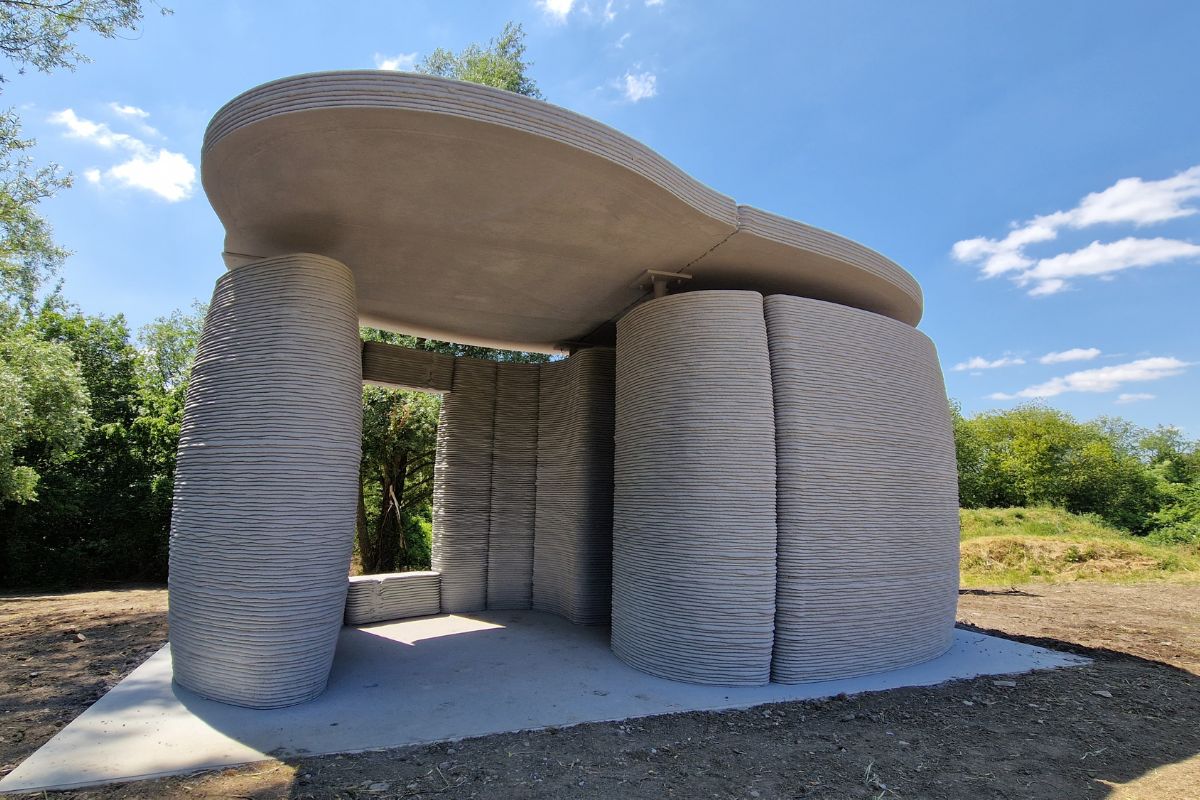
© MENSE-KORTE 2025
Innovative 3D printing is predicted to drive progress in construction like no other process. Not only does it enable the implementation of individual geometries and building components made of concrete that would not be possible with conventional formwork techniques, it also optimises the manufacturing and fabrication processes, thus enhancing the trend towards digitalisation in the construction industry. The construction of a 3D-printed “Tiny House” in North Rhine-Westphalia marks the culmination of a project that also relied on the use of sustainable building materials for the printing process. Together, Röser GmbH, a company based in Laupheim that specialises in 3D-printed prefabricated parts, MC-Bauchemie as an international developer and manufacturer of construction chemical products, and planning engineers MENSE-KORTE from Germany’s Münsterland region succeeded in bringing this visionary building project to fruition in 18 months.
Tiny House for bikers
The Tiny House is located on the grounds of a biker track in Beckum. With its large storage room including a roofed, open entrance area, the mini building offers the children and young people enough space on site to store tools and equipment for the sports facility. The Tiny House is equally impressive from the outside. Its elliptical façade curves outwards to merge directly with the vertical structure of the inner shell in a unique design only made possible by the 3D printing process.
Prefabricated parts from the 3D printer
The Tiny House design was developed with the help of modelling software. In addition, numerous material tests were performed to find the right composition suited to the requirements of the project. The finished concept was then fed into the so-called slicer software of the 3D printer. The next stage involved fabricating the individual segments of the building at Röser’s 3D printing site in Laupheim. The parts were subsequently transported over 500 kilometres from Laupheim to Beckum on a closed inboard loader – a real challenge given the size and intricate shape of the concrete components. "At first glance, the long transport route contradicts the targeted CO2 reduction, but we deliberately wanted to subject the 3D prefab elements to this stress test as part of the ‘premiere’," explains Dennis Bräunche, Röser’s technical field sales consultant responsible for the project. Once on the construction site, the prefabricated parts merely had to be placed on a precast concrete slab and connected to each other with the designated fixings, which meant that the Tiny House was ready for handing over to its owner within just a few hours.
Cement-free 3D-printing mortar with 70% less CO₂ emissions
MC-Bauchemie has been conducting research in the areas of 3D printing and sustainable solutions for the concrete and construction industries for many years now, gathering expertise that provided an ideal basis for the Beckum project. To meet the requirements of high-quality 3D printing, the material used needed to exhibit thixotropic behaviour – i.e. be deformable and pumpable as energy is input into the mixture, while remaining stable in the absence of such energy. The special 3D dry mortar used was MC-PowerPrint GeCO₂, which – in addition to good pumpability – also exhibits the necessary thixotropy and stability to enable an attractive and uniform print outcome after several slices, without undergoing deformation due to its own weight. MC-PowerPrint GeCO₂ features an additive-enhanced binder system comprised of blast-furnace slag and fly ash as an alternative to cement. "Overall, the use of alternative binders based on industrial by-products can save around 70% of CO₂ emissions compared to cementitious mortar products," says Kai Markiefka, product manager at MC, underlining the significant reduction achieved in the carbon footprint of this innovative technology.
Future-oriented building standard
The project in Beckum was a complete success, thanks in particular to the exemplary willingness of all involved to closely collaborate and effectively innovate. "Going forward we will need to further elaborate the 3D printing process so as to fully exploit its potential for construction as a viable and sustainable building standard," explains Waldemar Korte of planning engineers MENSE-KORTE, "In this way, we should soon be able to implement ever larger building typologies with a wide variety of uses. It is also crucial to keep optimising and diversifying pressure mortars to deliver ever more sustainability in the building process."
RELATED CONTENT
-
News
Click here to go to our News section.
-
MC-Pedia
In our MC-Pedia you will find technical articles on various topics written exclusively by our specialists.
-
Magazine
Get our latest issues of our customer and employee magazine MC aktiv.
-
Downloads
Find all relevant datasheets of our products as well as brochures of our company, Fields of Expertise and product categories here.
-
References
Click here to get to our library with reference projects for all types of application.
-
Careers
Click here to go to MC Career.
-
Contact
Click here to go to our Contact section.