-
Special Feature
Innovative solutions for the concrete industry
The Concrete industry sector is faceing significant challenges. High CO₂ emissions from cement production, scarce resources such as sand, and increasingly stringent environmental regulations are driving the need for innovation. Sustainable and forward-thinking solutions are more in demand than ever.
Concrete in transition – sustainable and specialty concrete
Apr 24, 2025
Concrete is the backbone of the construction industry and will remain indispensable for industrial, infrastructure and high-rise construction in the future. Rapid urbanisation is driving the demand for housing and infrastructure, further increasing the need for concrete. However, the industry faces major challenges. One of the key issues is the high CO₂ footprint of cement production – and consequently, concrete manufacturing. Additionally, the scarcity of natural resources such as sand and aggregates as well as their contamination present further challenges. Stricter environmental regulations and the European Emissions Trading System (ETS2) are also putting increasing pressure on the industry to innovate. To tackle these challenges, sustainable and innovative solutions are required – an area where MC-Bauchemie’s expertise in concrete technology is already making a significant impact.
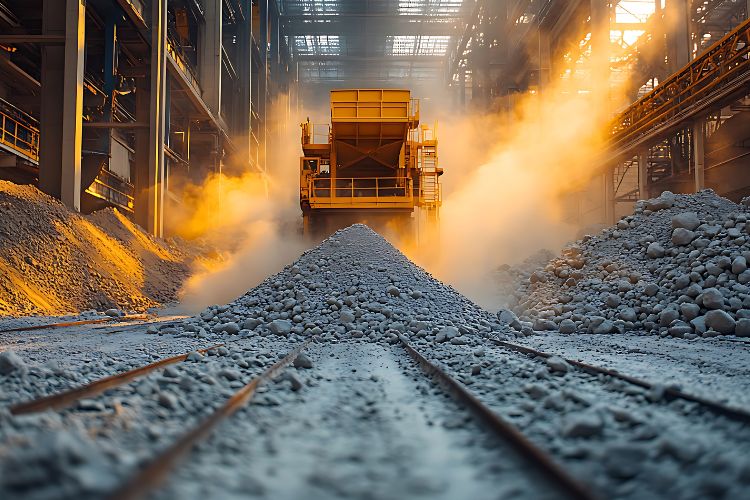
© blu – Gesellschaft für nachhaltige Immobilienprojekte mbH, Miguel Ferraz,
The concrete industry must drastically reduce its CO₂ emissions. As the construction sector plays a key role in global climate strategies, innovative approaches are essential to both minimise environmental impact and meet the growing demand for building materials. Companies are implementing various measures to establish more sustainable production methods. Modern cement plants are increasingly investing in CO₂ capture and recovery technologies to reduce emissions directly at the source. The use of alternative fuels and energy-efficient production methods can further reduce the ecological footprint of cement manufacturing.
CO₂ reduction and sustainability in concrete
The development of CO₂-reduced and climate-friendly concretes with little to no clinker content is a major focus of research. Through innovative formulations and alternative binders, CO₂ emissions can be significantly reduced compared to conventional concrete without compromising technical performance. More than a decade ago, in collaboration with Australian company WAGNERS, MC-Bauchemie developed a cement-free concrete known as EFC (Earth Friendly Concrete). This geopolymer concrete offers exceptional compressive strength, high sulphate resistance (XA3) and increased acid resistance. In fact, sulphate exposure further strengthens the material, enhancing its durability. This makes EFC ideal for structures exposed to harsh chemical conditions. MC-Bauchemie provides activators for EFC, which alkalise the alternative binders, such as ground granulated blast-furnace slag and fly ash used in place of cement. Additionally, a newly developed polymer improves workability. EFC has received its first general technical approval (AbZ) from the German Institute for Building Technology (DIBt) for use in precast concrete elements. It is also being used for Germany’s first cement-free concrete wastewater pipes, which have been available under the "next.beton" brand for over two years.
EFC was also used in the new construction project "4HÖFE" in Norderstedt from 2023 to 2024. In this project, all 800 m³ of precast elements and 2,200 m³ of ready-mix concrete were produced without cement, enabling the construction of approximately 300 apartments, including 71 climate-friendly social housing units built using timber skeleton construction. By using EFC, up to 75% of CO₂ emissions were saved compared to conventional concrete.
Additionally, the use of recycled and eco-friendly raw materials is continuously increasing. Concepts such as Urban Mining – the reuse of building materials from demolished structures – and the use of recycled concrete (R-concrete) are gaining importance. These approaches not only conserve natural resources but also reduce dependence on primary raw materials and minimise landfill waste, though their usage remains limited so far.
Concrete made from 100% recycled aggregate
MC-Bauchemie’s concrete technologists played a key role in developing concrete made entirely from 100% recycled aggregate. This innovative mix was first used in 2024 for the construction of a school building in Hamburg (see MC aktiv 1/2024). One major challenge of R-concrete is the higher water absorption of recycled aggregates. However, by combining the classic concrete admixture Centrament N9 with MC-PowerFlow evo 530, using MC’s latest PCE technology, the workability of the concrete was optimised. As a result, the concrete could be transported, processed and compacted just as easily as conventional concrete. This project impressively demonstrates how innovative concrete technology strengthens the circular economy while preserving natural resources like stone and gravel.
High-quality recycled concrete with a lower CO₂ footprint in the Netherlands
In the Netherlands, the company Urban Mine specialises in the production and supply of sustainable, high-quality recycled concrete that maintains the same quality, composition and properties as concrete made from primary materials. Urban Mine utilises MC-Bauchemie’s expertise and specially developed concrete admixtures for R-concrete and has over 15 years of experience in recycling concrete demolition waste. The Dutch company has perfected the recycling process in the Netherlands. The concrete is 100% circular and, according to the manufacturer, produces up to 80% fewer CO₂ emissions than conventional concrete. The company recovers concrete from demolished buildings and recycles it in an energy-neutral process using solar power and rainwater collection.
Composite cements with calcined clay
With the increasing demand for sustainable building materials, composite cements are gaining importance. Alternative materials like calcined clay are being used as substitutes for traditional Portland cement clinker. Composite cements with calcined clay offer multiple advantages – most notably a significant reduction in CO₂ emissions.
Since the calcination of clay occurs at temperatures between 600 and 850 °C, the energy requirement is much lower than that of traditional clinker production, which requires temperatures of around 1,450 °C. This leads to major energy savings and a significant decrease in CO₂ emissions.
However, there are challenges associated with using calcined clay in cement. Workability can be affected depending on the binder composition, and some applications may experience mechanical limitations.
MC-Bauchemie’s specialised additives as a solution
To ensure the performance and workability of concrete made with new composite cements, innovative concrete admixtures are essential. MC-Bauchemie’s special additives, when combined with PCE-based superplasticisers, act as "sacrificial polymers". Field tests have shown that these additives not only improve the flow properties of the concrete, making processing easier, but also ensure consistently high concrete quality.
The importance of such technologies will continue to grow in the future. The market is moving towards more climate-friendly concretes, such as EFC or R-concrete, which enable a more sustainable approach to construction. MC-Bauchemie’s specialty additives not only provide solutions for current applications but also support future developments, such as Urban Mining and the increased use of recycled building materials. Furthermore, this technology improves the workability of concrete when using sands containing clay or lower-quality sands.
Specialty and sustainable concrete – not without concrete chemistry
To meet these challenges, the concrete industry must invest in research and development, adopt new technologies, and collaborate closely with research institutions and construction chemistry manufacturers. The future of the industry lies in the development of sustainable, intelligent and efficient concrete solutions that meet the evolving demands of both the market and society.
MC-Bauchemie is a leader in this field, already setting tomorrow’s standards with innovative technologies and sustainable solutions – whether for EFC, R-concrete, new cement types or contaminated aggregates and sands. With its extensive expertise, MC’s concrete technologists provide robust and reliable solutions for all these challenges and future developments.
RELATED CONTENT
-
News
Click here to go to our News section.
-
MC-Pedia
In our MC-Pedia you will find technical articles on various topics written exclusively by our specialists.
-
Magazine
Get our latest issues of our customer and employee magazine MC aktiv.
-
Downloads
Find all relevant datasheets of our products as well as brochures of our company, Fields of Expertise and product categories here.
-
References
Click here to get to our library with reference projects for all types of application.
-
Careers
Click here to go to MC Career.
-
Contact
Click here to go to our Contact section.