-
Special Feature
CEMENT-FREE INTO THE FUTURE
Sustainability in construction is vital, and MC is pioneering eco-friendly solutions, aiming to reduce cement-related CO₂ emissions with new technologies.
MC research focusing on sustainable construction
Nov 22, 2024
For years, the issue of sustainability has played a key role in the construction industry – and cement manufacturing in particular is increasingly becoming the focus of attention due to the CO₂ emissions that it causes. The development of cement-free building materials should help to significantly improve the entire industry’s carbon footprint going forward. MC is at the forefront of research in this area and is already developing tomorrow’s standards for today with new technologies and sustainable solutions.
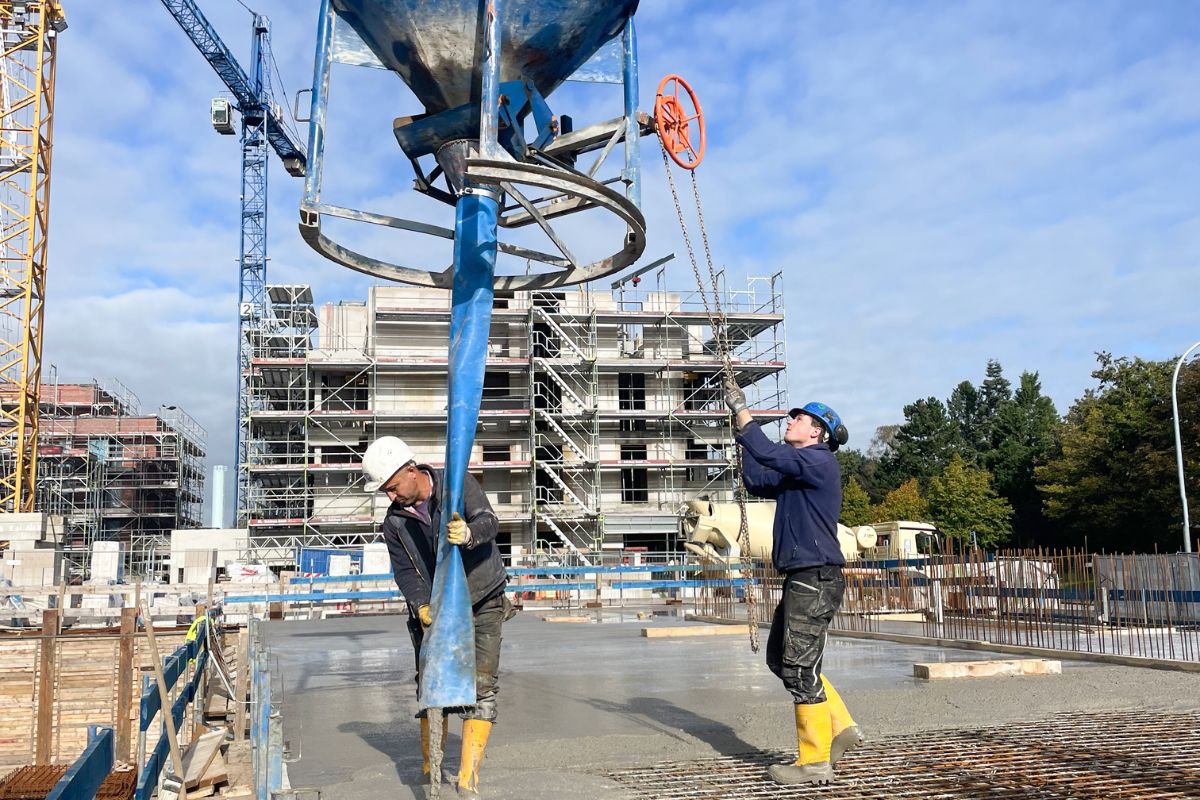
© blu – Gesellschaft für nachhaltige Immobilienprojekte mbH
Nothing works in construction without concrete: Around 14 billion m³ of concrete are used worldwide every year. This requires cement. During its production, CO₂ is released as a result of the conversion of natural carbonate into clinker, with additional energy then required to calcinate (burn) and grind the clinker to form cement. In 2023, an estimated 4.1 billion metric tons of cement were produced worldwide. Cement production released almost three billion metric tons of CO₂ – and therefore currently accounts for around eight percent of total man-made carbon dioxide emissions. Significantly, up to 95 percent of concrete’s global warming potential is dominated by the CO₂ emissions associated with cement production. In order to achieve the European Union’s Paris climate targets and thus climate neutrality by 2050, the construction sector must drastically reduce its emissions over the next two decades. In this context, building owners are also increasingly focussing on sustain-able construction and striving for the best possible DGNB or similar sustainability certification for their buildings. Large companies and local authorities in particular are stepping up their efforts to save CO₂. As a result, interest in cement-free concretes is growing continuously – throughout Europe.
The path to net zero: Cement-free concrete
Research into alkali-activated binder systems as cement substitutes has been going on for more than 100 years. Since the 1970s, research into geopolymers as binding agents has been intensified. However, a real breakthrough has only recently been achieved by the Australian company Wagners with EFC® (Earth Friendly Concrete®), a geopolymer binder based on secondary raw materials such as blast furnace slag and fly ash. EFC® contains no cement and therefore causes significantly lower CO₂ emissions. Instead, blast furnace slag from pig iron production or other clinker substitutes are used. Special activators and concrete admixtures are added, which come from MC and are customised to the individual application. However, Earth Friendly Concrete® is by no means just a ‘concrete substitute’ – but rather a new building material with a number of specific advantages. The absence of cement in the concrete mix means a reduced amount of calcium hydroxide and therefore less reactivity with other materials. This results in a more resistant concrete, especially to chemical attack (exposure class XA3). As a result, there is generally no need for additional coating or lining of components. In addition, cement free concrete has a CO₂ footprint that is up to 75 % lower than conventional concrete.
MC-Bauchemie performing pioneering work
MC has already been heavily involved in furthering the product maturity of Wagners’ EFC® with its Research & Development department working on the concrete formulation and developing special active tors and superplasticisers to achieve the application properties required for efficient EFC® installation. The resulting geopolymer concrete mix is also, in the final analysis, the result of ten years of development work at MC. In a first major project in 2014, EFC® concrete was used in the expansion of Brisbane Westwellcamp Airport – for 51,000 m² of heavy-duty pavements in the provision of turning pads and taxiway areas, as well as for the foundations and wall slabs of the terminal building. And in this project alone, around 8,800 metric tons of CO₂ emissions were saved through the use of EFC®.
.
EFC® with German Institute of Building Technology (DIBt) approval
Under reference Z-3.15.2157, the German Institute for Building Technology (DIBt) issued a general building approval (AbZ) for the first time for EFC® as an alternative for precast concrete elements. This laid the foundation for the first German production of a cement-free binder compound by Holcim Deutschland GmbH. MC also played an important role here, as the compound made from secondary raw materials such as slag or ash produced as miner-al by-products in other branches of industry, can only fully replace cement thanks to the activator developed by Wagners and MC. Moreover a high performance superplasticiser series that is ideal for use in geopolymer concrete – namely MC-PowerFlow 4100 – was developed in the MC laboratories in Bottrop. This flow-enhancing product has been specially ap-proved for binder combinations of ground granulated blast furnace slag and fly ash and ensures strong liquefaction with economical dosing. The specific functional mechanism enables the production of high-performance cement-free concretes with excellent application properties and without segregation and bleeding.
Major project with MC-PowerFlow 4100
Earth Friendly Concrete® was used on a large scale between 2023 and 2024 in Norderstedt for the 4HÖFE new-build project. This involved around 300 apartments being built on four construction sites in the city centre. In order to examine the potential for reducing CO₂ emissions in social housing in more detail, blu – Gesellschaft für nachhaltige Immobilien-projekte mbH, a subsidiary of Hamburg-based AUG. PRIEN Bauunternehmung (GmbH & Co. KG), had 71 climate-friendly social housing units built on one of the four construction sites using a timber frame construction method combined with geopolymer concrete – a construction method that gave the project showcase status throughout Germany (as reported in MC aktiv 3/23). Here, too, the high-performance superplasticiser MC-PowerFlow 4100 was the first choice for the cement-free concrete so as to optimise the application properties both for the precast elements from prefabricator fdu GmbH & Co. KG, and for the ready-mixed concrete, which was produced in co-operation between Betonlift GmbH & Co. KG and Betonlabor Süderelbe GmbH & Co. KG, with a view to ensuring accurate formulation of the concrete. The result not only impressed the client: Compared to reference concretes based on cement as a binding agent, the EFC® resulted in CO₂ savings of up to 75 %. This is also confirmed in terms of global warming potential (GWP), as determined by a life cycle assessment (LCA) conducted by certification agency KIWA.
Sewerage system constructed using next.beton
Zementrohr- u. Betonwerke Karl Röser & Sohn GmbH is also capitalising on the development of cement-free concretes. Together with Berding Be-ton GmbH and Finger Baustoffe GmbH, this Mun-delsheim based company is launching its next. beton piping onto the market as ‘Germany’s most climate-friendly sewerage system’. The next.beton products are made from a cement-free geopolymer concrete instead of conventional concrete. Here too, MC-Bauchemie was able to successfully shape the associated product development and optimisation. The cement-free concrete technology not only offers considerable CO₂ savings potential of up to 75%, it also conserves primary raw materials – without any impairment to the technical and structural qualities of the product. On the contrary, in fact: The pipes made from next.beton are characterised by high resistance in accordance with exposure class XA3 and can thus be used without the additional protective measures that would otherwise be required.
3D printing: Houses from the printer with EFC®
We are currently experiencing a step into the future of construction with 3D printing involving concrete as the core material. Instead of being built brick by brick, houses are created using a 3D printer. They not only look good with their sometimes futuristic touch, they are also extremely cheap and quick to build. The potential for this construction technology is currently regarded as being streets ahead of any other process. And advancements in Germany are occurring at breakneck speed: In Beckum, Westphalia, the first Tiny House from the printer has been created with cement-free concrete – with MC-PowerPrint GeCO₂, a cement-free binder-based mortar for 3D concrete printing. Planning engineers MENSE-KORTE from Münsterland and Röser GmbH from Laupheim, which specialises in 3D-printed prefabricated parts, drove this pioneering construction project together with MC. The task assigned to MC’s experts was to develop a product in the shortest possible time that offered both the required properties, such as those relating to strength, and the processing behaviour necessary for 3D concrete printing – while also significantly reducing the carbon footprint of the overall process. The result after just one year: MC PowerPrint GeCO₂, a mortar for 3D printing. As MC-PowerPrint GeCO₂ can also be used with an additive system of granulated blast furnace slag and fly ash as an alter-native to cement, up to 70% of CO₂ emissions can be saved compared to cementitious mortar products. MC-PowerPrint GeCO₂ offers ideal thixotropy for this technology, i.e. the mortar is liquefied under the in-fluence of energy, for example when pumped by the printer, and is therefore easy to pump and mould, but becomes stable once the mechanical influence is ab-sent. This results in a fine, uniform printed shape that undergoes no deformation from the effects of its own weight, even after several layers of printing.
CO₂ reduction not just in concrete
The experts at MC are working on combining new technologies and sustainable solutions in order to reduce or even eliminate cement consumption in as many areas as possible. MC’s portfolio ranges from special cement-free applications such as annular space grouting mortar in tunnelling, surface protection systems, solutions for waterproofing buildings and the world’s first cement-free moisture control render, to ‘everyday’ building products such as cement-free mortars or clinker-reduced systems for floor construction. The latter are already being successfully marketed by Botament, a sister company of MC, under the brand name BotaGreen. Moreover, all BotaGreen products carry the EC1PLUS mark, the highest possible EMICODE® seal of approval within the product classification for low-emission installation materials and building products.
Eyes cast to the future
Already on the horizon are further projects likely to form an integral part of everyday construction site life in the near future. These include innovative paving stones and roof tiles, for which MC has developed a functional, semi-dry, cement-free formula for production of the core concrete. Such alkali-activated building materials also offer real added value for these stoneware products: They achieve higher strength values than concrete, are more resilient and, unlike conventional paving products and roof tiles, are not prone to limescale (aka chalk) efflorescence.
The innovations and solutions presented here show that the range of cement-free alternatives available for building materials is becoming ever more diverse. It is also becoming increasingly clear that important contributions can be made in the construction sector to significantly improve the carbon footprint of the entire industry and thus assist in securing the future of mankind. Whether Earth Friendly Concrete®, geo-polymers, 3D printing or the replacement of cement in other building materials, MC’s ongoing research and development effort is helping to meet the increasing demands of the construction industry with innovative and sustainable solutions. With cement-free products and technical support from experienced experts and consultants, MC plays a leading role in the field of sustainable building materials – and is already devel-oping tomorrow’s standards today.
RELATED CONTENT
-
News
Click here to go to our News section.
-
MC-Pedia
In our MC-Pedia you will find technical articles on various topics written exclusively by our specialists.
-
Magazine
Get our latest issues of our customer and employee magazine MC aktiv.
-
Downloads
Find all relevant datasheets of our products as well as brochures of our company, Fields of Expertise and product categories here.
-
References
Click here to get to our library with reference projects for all types of application.
-
Careers
Click here to go to MC Career.
-
Contact
Click here to go to our Contact section.