-
Special Feature
Top products for better screeds
Screed goes beyond flooring, enhancing industrial load-bearing and offering insulation in homes. MC-Bauchemie provides specialized systems for various needs.
Screed Systems - Top products for better screeds
Jan 10, 2024
Screed continues to grow in importance in construction – and not just as an essential basis for the subsequent floor covering. Screed fulfils an important function in the industrial sector by enhancing the load-bearing capacity of the floor. In residential construction, meanwhile, the multi-layer system provides footfall-sound insulation and a heat-insulating layer to prevent energy losses. Within its Screeds product family, MC-Bauchemie offers various screed systems to optimise the properties of this base layer according to the task at hand.
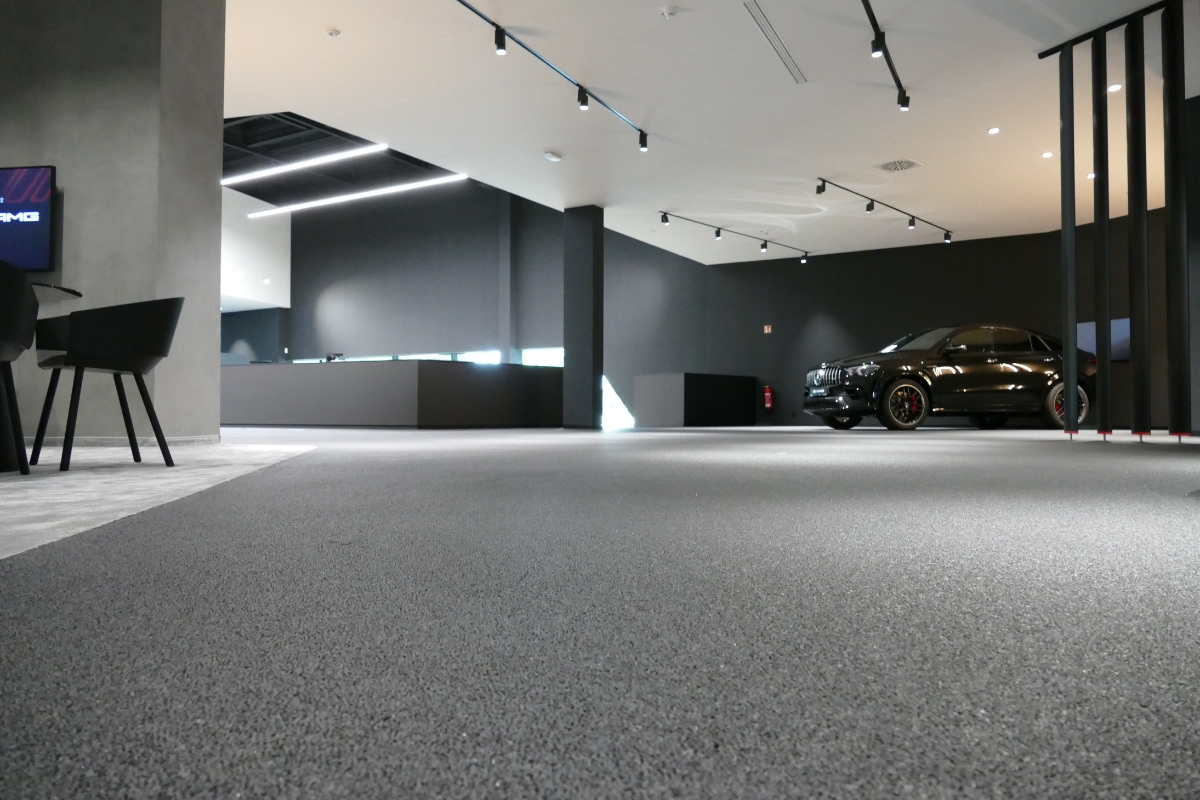
© MC-Bauchemie 2024
Screed is used today in a large number of variants. The general standard DIN EN 13318 basically defines screed as a layer or layers of screed mortar that is or are laid on the construction site directly on the substrate, with or without a bond, or on an intermediate separating or insulating layer. The screed fulfils two tasks. It ensures the required evenness of the floor and accommodates the intended floor covering. The specific requirements placed upon it depend on the intended use and the associated stress profile in each individual case. Other important factors include the surface covering, the planned construction times and, last but not least, conditions encountered on the construction site.
The initial criteria applied in specifying the screed derive from the installation: bonded screed adheres directly to the load-bearing concrete and can withstand particularly high loads. It is used in industry and sometimes also in basements. In living spaces, on the other hand, screed is laid without any direct adhesion to neighbouring building components. This “floating” construction is the norm in Germany due to the requirements prevailing for sound and heat insulation.
The five types of screed
Screeds are primarily differentiated by the binder that is added to the screed mortar. Cement screed (CT) is currently the most common type of screed. It is used indoors and outdoors and offers a wide range of applications, but generally requires a long drying time. Calcium sulphate screed (CA), also known as anhydrite screed, is almost exclusively installed as a levelling or free-flowing screed. It is characterised by good thermal conductivity, low residual stress/distortion and the ability to produce very even surfaces. This makes it more suitable for use in large jointless areas and in areas where underfloor heating is planned. Synthetic resin screed (SR), which is produced with epoxy resin, is extremely robust. It is not only resistant to heat and cold, but also to many chemicals. It is therefore also suitable for industrial floors that are exposed to high stressing. Magnesia screed (MA) is a less common alternative for industrial floors that are subject to particularly high stressing. It offers both high strength and high load-bearing capacity. Mastic asphalt screed (AS), which uses bitumen as a binder and must be applied at temperatures of around 250°C, is also used less frequently.
Screed systems from MC – always a safe choice
In Germany, cement or calcium sulphate screeds currently predominate in new buildings. The Screed division of MC-Bauchemie offers a comprehensive portfolio of product systems, particularly in the area of cement screed. Depending on the requirements, these can accelerate the drying of the cement screed, improve workability, ensure high early strength and final strength for early readiness for covering and rapid trafficability, or ensure a good adhesive bond. Tim Hillringhaus is responsible for screed systems at MC. He has been Global Product Manager since the beginning of 2016 and Head of Screed Sales since the beginning of 2020. Since then, he has been driving the product division forward, particularly in Germany, which is divided into two segments: products for the production and improved application of screed, and special solutions for the repair and finishing of screed floors. The portfolio ranges from screed accelerators and rapid cements to floor levelling compounds, coating and finishing systems and repair systems.
Improving the workability and application properties of screed
“In this field, it is all about improving the application properties of cement screed,” explains Tim Hillringhaus. “Whereas concrete is supplied from the plant to the construction site ready to use, in the case of screed it is the raw materials that are delivered. Charged into a mixing and conveying unit, this is turned into screed mortar, which is conveyed directly to the application site.” This is where the MC products come in. Pumping over long distances can be a challenge. While a hose length of 40 metres is quite commonplace, it can rise to around one hundred metres on large construction sites. Pumping the mortar over such distances is only possible with additives such as MC-Easyscreed. This highly concentrated application aid for cement screeds improves the pumping behaviour of semi-dry screeds and ensures a significant improvement in their workability resulting in a significantly higher laying performance. “We once had a construction site where the screed mortar was pumped over 180 metres – it was in the hose for seven minutes,” recalls Hillringhaus. In this case, MC-Easyscreed was the only product able to maintain the pumpability of the screed from start to finish.
Accelerated drying
Alongside workability, the drying behaviour of the screed is a further key consideration, determining as it does the speed with which a screed can receive operational loading and how quickly it is ready for covering. “This is a classic area of concern and one that is constantly open to improvement. When has the screed reached its specified residual moisture content? When is it suitable to receive the floor covering? A standard cement screed can take six to eight weeks to dry out after installation, and even longer in adverse environmental conditions. This is a test of patience for private builders – and a real no-no for housing associations or in industry,” explains Hillringhaus.
The shrinkage-reducing screed accelerators in the MC-Powerscreed series for semi-dry cement screeds can reduce the drying time to between seven and 14 days – an enormous time saving and a clear advantage for builders. And that’s not all: the screed is also easier to compact and scores highly in terms of strength, allowing the layer thickness of the screed to be reduced. This not only makes it possible to compensate for a planning error in terms of floor height, it also increases cost-efficiency: for if, say, only 5 cm of screed needs to be heated instead of 8 cm, the savings on material, time and money can be huge.
Ternary binder for special applications
With MC-Floor TurboCem, MC has developed a special binder that can be used in a variety of ways. It can be applied as a rapid cement for residential construction as well as for the production of industrial screeds or high-strength commercial screeds – both indoors and out. The screed properties can be controlled with this one-for-all product by adjusting the dosage to specific application requirements. This is a great advantage for screed layers, as it makes handling easier and reduces the complexity of storage, transport and, above all, application. In addition, MC-Floor TurboCem requires less cement for the screed mix, which also saves on cost compared to conventional rapid cements.
As this special ternary binder – which came onto the market in 2020 – chemically binds significantly more water, only a small proportion of the mixing water used needs to evaporate. This means that readiness for covering can be reliably achieved within a few days even under critical ambient conditions, and covering readiness values of between three and 14 days can usually be realised without problem. MC-Floor TurboCem offers a working time of ≥ 90 minutes for screeds of quality class C30-F5; it can be walked on after twelve hours and is ready for covering after ten to 14 days. For C50-F7, it offers a working time of ≥ 45 minutes, can be walked on after six hours and is ready for covering after three days*. “Our quick-setting cement also has the advantage that it hardens with extremely low residual stress, ensuring good dimensional stability. It further fulfils the criteria for SW1 screeds in accordance with DIN 18560,” says Tim Hillringhaus.
Reliable screed repairs
MC’s screed portfolio also includes a number of repair systems. Even when screeds are laid correctly, cracks can sometimes occur near the surface or even through the entire cross-section. If these are not repaired, they can cause serious failure at a later date. “Procedures do not always run smoothly on a construction site, things can go wrong here and there – and then the screed has to be repaired,” says Hillringhaus. In such cases, MC-Bauchemie offers MC-Estrifan, a range of products with which cracks in screeds can be rigidly and permanently closed. The two-component reaction resin MC-Estrifan RIS-SL, for example, can be used to repair cracks and close joints quickly, cleanly and safely. Application is extremely simple: the base and hardener components are mixed in the bottle and then simply poured into the crack or joint.
Levelling and protecting the screed
In other cases, an uneven screed may need to be levelled. “A certain depth and clearance must always be maintained so that the doors still open. The screed also needs to be levelled so that tiles, for example, lie flat. Nobody wants to have a motocross track in their living room – everything needs to be nice and straight,” explains Hillringhaus with a smile. MC also has the necessary levelling compounds in its range, such as MC-Floor Easyplan classic, which enables the levelling of uneven cement screed and concrete floors both indoors and out.
Products for surface protection and surface finishing also belong in this category. “These are not only used in industry,” emphasises Hillringhaus, “but also in residential construction. The classic example here is the basement. Hardly anyone lays tiles there these days unless they have money to spare. A simple coat of paint is enough to make the floor easier to clean and look good.” Various products are also available here, such as MC-Estrifan SI impregnating agent for finishing mineral surfaces, or the pigmented MC-Estrifan Color Protect floor sealer. As coatings to enhance floor resilience, MC also offers the transparent universal resin MC-Estripox pro and the epoxy resin coating MC-Estripox protect.
In conclusion
Summarising the current situation, Tim Hillringhaus comments: “As a topic, screed was hardly ever discussed, even in the construction industry. It was simply ‘the grey slab you have to have’. Today, people understand how much science is behind it – and what possibilities screed can offer with our speciality products.” MC’s portfolio is very broad. It not only offers solutions for practically all requirements, but also many advantages for everyone involved in the construction process. Builders and clients in residential construction benefit from shorter drying times and the resulting reduction in construction time. Builders and clients in the industrial sector benefit from a screed that is of a particularly high quality and has a much higher strength and resistance than the standard screed, as well as from the sometimes massive time and therefore cost savings during installation. And last but not least, screed layers benefit from easier application and higher productivity in terms of square metres per day.
* All figures are based on a temperature of 10 °C and a relative humidity of 80 %.
Related Products
-
News
Click here to go to our News section.
-
MC-Pedia
In our MC-Pedia you will find technical articles on various topics written exclusively by our specialists.
-
Magazine
Get our latest issues of our customer and employee magazine MC aktiv.
-
Downloads
Find all relevant datasheets of our products as well as brochures of our company, Fields of Expertise and product categories here.
-
References
Click here to get to our library with reference projects for all types of application.
-
Careers
Click here to go to MC Career.
-
Contact
Click here to go to our Contact section.