we help you?
-
Sustainability
Energy revolution: winding up the wind - powerful, efficient, sustainable
Wind power is one of the most promising sources for climate-neutral energy. Wind turbines now rotate in more than 100 countries around the globe, providing a sustainable power generation. MC-Bauchemie offers a wide range of high-performance products and innovative systems for those turbine structures.
Wind power - a powerful and sustainable energy source
Sep 13, 2021
Wind power continues to carry our hopes for climate-neutral energy generation. The associated technology has developed rapidly in recent years. Modern, powerful wind turbines now rotate in more than 100 countries around the globe. MC-Bauchemie offers a wide range of high-performance products and innovative systems for the manufacture, installation, protection and renovation of the associated turbine structures.
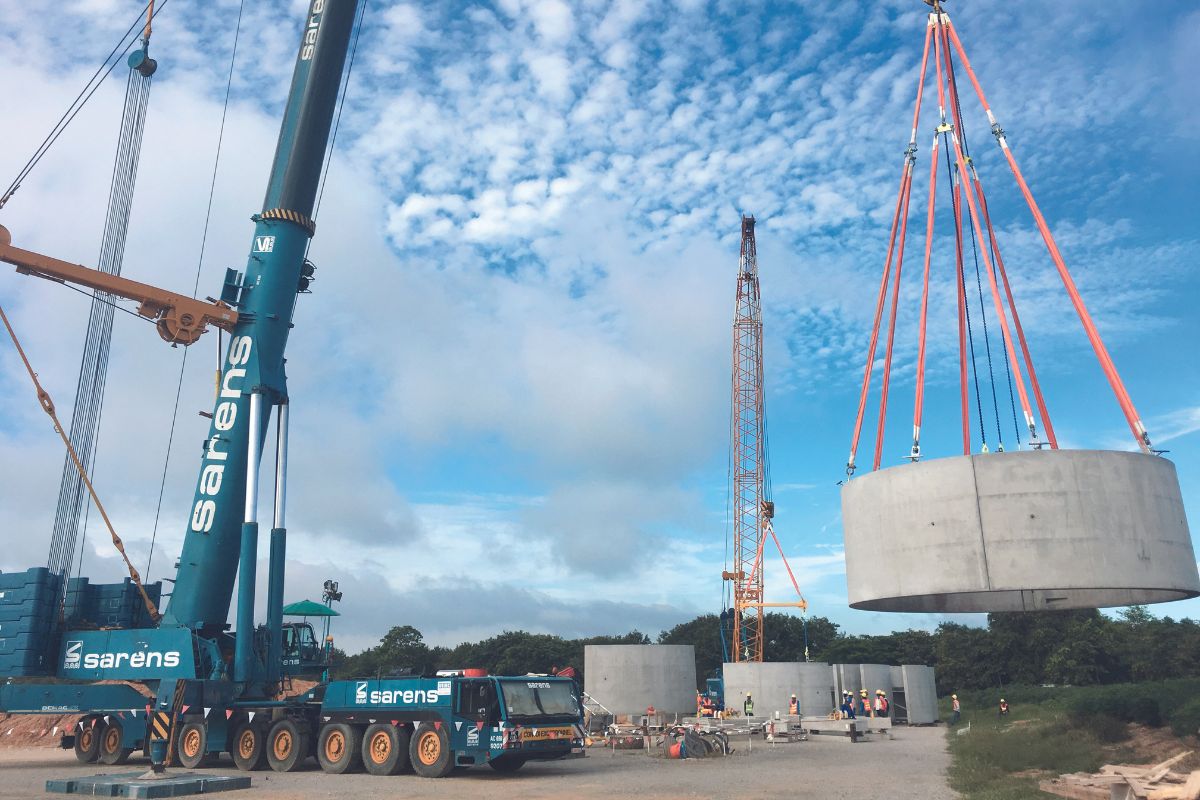
Wind energy is currently being farmed and commercially utilised in 103 countries around the world. The global output of wind power overtook that of nuclear energy in 2015, since which time it has further extended its lead. In 2018, wind energy accounted for over 8 % of total global electricity consumption. And in the past three years alone, the output of wind turbines erected worldwide has grown from around 590 to over 740 GW. The frontrunners in this expansion are China, the USA and Germany – as they have been for almost a decade now. Wind power is booming – right around the world. In Europe, wind energy now boasts the largest power plant capacity of all electricity generation sources. A total of 220 GW of wind energy capacity has now been installed in Europe, of which 195 GW is onshore and 25 GW offshore. In 2020, wind turbines in Europe generated a total of 458 TWh, or 16 % of total electricity consumption. In 2020, the share of wind energy in the electricity mix in Denmark, the EU leader, was 49 %, followed by Ireland with 38 % and Germany and the United Kingdom, each with 27 %. And the wind energy industry remains on a decidedly upward trajectory.
MC’s “Wind Power” Field of Expertise
For many years now, MC has offered a broadbased product portfolio for this booming market, from solutions for concrete foundations and precast concrete parts, to high-performance protection, coating and concrete repair systems. MC has pooled all its expertise in the construction and maintenance of wind turbines within its Wind Power FoE (Field of Expertise). In addition to high-performance products and innovative systems, MC’s highly qualified team offers comprehensive off- and on-site support with everything from product application training to implementation assistance. The technological progress made since 1979 – when the first series production of wind turbines began in the Netherlands – has been immense. While the output of a wind tower in the 1970s was just a few kilowatts, the 1980s and early 1990s saw technological advancement from small (50 kW to 150 kW) to medium-sized wind turbines (500 kW and 600 kW). The start of the new millennium then heralded the advent of the megawatt class. Newer wind farm installations are typically rated at four to six megawatts – enough electricity to supply several thousand households. For further information on MC's field of expertise "Wind power", take a look at our website.
Wind Power:Technology unchained
In the last 20 years, the technical development of wind power generation has mainly focused on the construction of ever larger turbines in order to achieve higher outputs per unit. By 2020, the average rotor diameter of new turbines in Germany had grown to 122 metres and the average hub height to 135 metres. But there was no stopping there: In order to achieve a high power yield even in areas with less wind, more and more so-called low-wind turbines have been erected in the recent past. Such units now have rotor diameters and hub heights of over 160 metres.
Base challenge
Such tall towers bring high demands on structure construction, starting with the laying of the foundation. When a wind turbine is erected on land (onshore), a round base made of steel-reinforced concrete is created which, due to its weight, lowers the overall centre of gravity of the structure. In addition, its diameter moves the tilting edge of the wind turbine so far away from its centre of gravity that the turbine cannot be overturned even by maximum wind forces acting on it. For example, for a turbine with a hub height of 141 metres and an output of 2.4 MW, the diameter of the foundation is 22 metres and the depth up to 4 metres. This means that around 1,300 cubic metres of concrete and 180 tonnes of steel will be required for its construction. Challenges associated with the large quantities of concrete involved – such as the high heat of hydration produced – and also adverse weather conditions during the construction phase can be effectively overcome with admixtures from MC such as the multifunctional superplasticisers from the Muraplast product line or the hardening retarders from the Centrament Retard range. And to avoid difficulties with the rate at which the concrete sets, MC also offers a wide selection of Emcoril curing agents.
Hybrid towers: Precast concrete components with optimised properties
MC products also increase productivity and performance in the manufacture of precast concrete components for wind towers. In the past, the towers were mainly made of steel, but today hybrid towers are increasingly the norm for tower heights beyond 100 metres. Steel tube towers of this size are no longer economical because of the material and maintenance costs involved. Hybrid towers, on the other hand, consist of concrete elements with a steel extension at the top. In the lower part, precast concrete elements – mostly tubular half-shells – are assembled and vertically prestressed with tension cables. Towards the top, the construction transitions to flanged steel tubes. With the high-performance PCE-based plasticisers of the MC-PowerFlow product range, Muraplast superplasticisers and also the latest generation of MC-FastKick hardening accelerators, MC provides admixtures for all requirements in the production of the precast concrete elements described.
Secure connections between concrete elements and bearing blocks in the foundation
Success in the construction of a wind tower also depends on ensuring a secure, rigid connection and bond between the precast concrete elements, together with effective curing of the grouting and sealing materials used. Emcekrete 80 and MC-DUR 1300 Plus offer the best technical properties for these applications and will even reduce crane operating times. MC-AnchorSolid E820 is the first choice for anchoring and bonding the zero-adjustment bearing blocks on the foundation of the enormous wind turbine masts, and also for grouting the resulting cavities. This highly reactive anchor adhesive has proved to be particularly durable and resistant. As a ready-to-use, two-component product based on epoxy resin, it is especially suitable for anchoring threaded rods and reinforcing steel in both dry and water-saturated, uncracked concrete. MC-AnchorSolid E820 is approved as an anchor bonding adhesive according to European Technical Assessment ETA-15/0506 and has been tested compliant for use in C 20/25 to C 50/60 concrete for anchoring threaded rods and reinforcing steel for mounting attachments. Even under demanding climatic conditions, with outside temperatures of up to 40 °C and high humidity, it has been proven to meet all requirements in relation to strength and tolerance.
Durable protection against external attack phenomena
Wind turbines are not only exposed to permanent stress loading due to vibration and movement; depending on the location, there may be additional attack phenomena arising from salt and abrasion that can damage the structure. With high-performance coatings from the MC-Color product range, the concrete of wind towers is able to permanently resist the effects of wind, CO2 and chlorides. MC-Color products are open to water vapour diffusion, flexible, highly resilient and fast-curing. The multitude of high loads and stresses to which a wind turbine is subjected in the course of its operating life means that concrete damage in the structure is always a possibility. And MC’s concrete replacement systems have all the attributes to provide the right repair solution. Indeed, MC’s Nafufill series is capable of meeting a wide range of requirements when it comes to reinforcing the damaged concrete of a wind tower, should the need arise. With Nafufill LM, Nafufill KM 220, Nafufill KM 230 and Nafufill KM 250, MC offers four repair mortars that not only fulfil the requirements of EN 1504 Part 3, but also give the planner peace of mind in the face of such critical refurbishment undertakings. MC likewise offers globally unique, effective, high-performance injection systems in the form of the MC-Injekt product family, enabling cracks and cavities in wind towers to be safely and permanently closed and sealed so as to avoid critical consequential damage. Wind power will continue to be an indispensable part of the energy mix worldwide for a long time to come – especially in view of global efforts to effectively and permanently reduce CO2 emissions. And that means that ever greater importance will be attached to the construction, protection and repair of wind towers. There is an urgent need to keep wind farm rotor blades around the globe constantly turning so as to ensure maximum cost- and resource-efficiency.
RELATED CONTENT
-
News
Click here to go to our News section.
-
MC-Pedia
In our MC-Pedia you will find technical articles on various topics written exclusively by our specialists.
-
Magazine
Get our latest issues of our customer and employee magazine MC aktiv.
-
Downloads
Find all relevant datasheets of our products as well as brochures of our company, Fields of Expertise and product categories here.
-
References
Click here to get to our library with reference projects for all types of application.
-
Careers
Click here to go to MC Career.
-
Contact
Click here to go to our Contact section.